There are many different concrete protection products on the market. As you can imagine, these concrete corrosion inhibitors and waterproofing methods are not all created equal.
That’s true even when you’re comparing products in the same category, such as the effectiveness of Hycrete versus other hydrophobic admixtures. However, it’s especially true when you look at the larger industry and consider just how different the various methods are for achieving waterproof concrete.
At the top you have Hycrete’s hydrophobic admixtures which repel water and prevent corrosion from reaching beyond the surface of the structure. In contrast, there are hydrophilic crystalline growth admixtures which actually rely on water ingress, essentially acting as densifiers to prevent future water intrusion. Then you have applied membranes which cover the outer surface of the structure with a physical barrier, “waterproof” surface sprays and treatments, etc… the list goes on.
In some of our previous blogs, we’ve already discussed why Hycrete’s advanced hydrophobic admixtures have been proven to be the most effective waterproofing strategy on the market:
Beyond being more effective, Hycrete makes concrete waterproof and protects against corrosion – both concrete corrosion and rebar rust. Many competing products require a separate concrete corrosion inhibitor, which complicates the mixing process and leaves the door open for subpar waterproofing results.
Before we delve further, it’s important to understand the reason why concrete structures require a waterproofing agent.
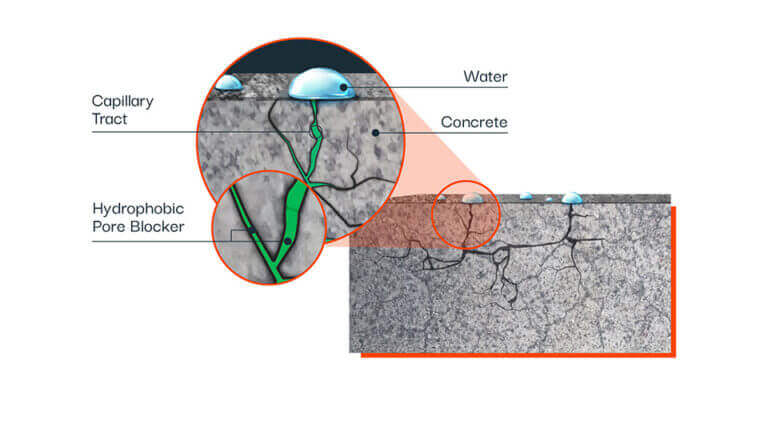
How Water Works Its Way into Concrete
Unfortunately, concrete is far from waterproof on a molecular level. Concrete materials come with an intrinsic porosity, and the chemical nature of the material constituents further open up the door for water ingress.
A Look Inside Concrete Materials
Concrete is a composite material composed of cement, water, and various aggregates such as sand and gravel. When water is added to cement, a series of chemical reactions known as hydration begins.
The reactions form calcium silicate hydrate (C-S-H) gel, which is the primary binder that gives concrete its strength. On the other hand, the hydration process tends to create microscopic capillary pores as water works its way throughout the material. These pores are the main reason why concrete isn’t waterproof after it hardens.
At the molecular level, the formation of these pores is tied to the imperfect packing of particles and the incomplete hydration of cement. Not all water used in the initial mix becomes chemically bound – some of it remains trapped within the material and later evaporates, leaving behind voids which serve as pathways for future water ingress.
Additionally, the C-S-H gel itself is not a crystalline solid but rather an amorphous, gel-like structure. That tends to create an uneven distribution with tiny pores and channels throughout. Even the smallest of these voids allow for water to migrate through the concrete via hydrostatic pressure, capillary action and diffusion.
Another factor is the presence of microcracks. These can form due to drying shrinkage, thermal stresses, or mechanical loads during the construction process. These cracks can act as conduits within the hydration pore network, facilitating water intrusion throughout the concrete. Even the smallest hairline cracks can dramatically increase permeability.
All of that is to say – it’s the fundamental chemistry and microstructure of concrete which make the material inherently non-waterproof at the molecular level.
Concrete Is Hydrophilic: The Opposite of Waterproof
Further complicating the process for builders, concrete is also a hydrophilic material. That basically means its molecular structure has an affinity for taking on water at the chemical level. The polar nature of water molecules allows them to be drawn into and through the concrete matrix.
Even when surface treatments are applied or the mix design is altered to reduce permeability, the material still cannot be made completely impermeable. At best, such modifications can significantly reduce the rate at which water permeates the concrete, but cannot eliminate it entirely. Enter Hycrete: a more comprehensive waterproofing solution that reduces water absorption to less than 1% while simultaneously acting as a corrosion inhibitor.
Concrete Waterproofing Methods and Corrosion Inhibitors Compared:
Hydrophilic Crystalline Growth Admixtures
Hydrophilic admixtures rely on concrete absorbing water to initiate a crystalline growth process. So technically, you could say “hydrophilic” concrete admixtures are actually the opposite of waterproof. These products therefore require a precise combination of hydrophobic and hydrophilic mixtures within the concrete to meet waterproofing specifications.
Calcium Nitrite-Based Corrosion Inhibitors
Calcium nitrite-based corrosion inhibitors are widely used in conjunction with hydrophilic admixtures, as well as with surface treatments and external membranes. The goal is to combine a waterproofing product with enhanced corrosion protection for the internal steel reinforcement. So calcium nitrite corrosion inhibitors are engineered to protect against the corrosive effects of water, not to make the concrete itself waterproof or water resistant.
Surface Treatments and Surface-Applied Corrosion Inhibitors (SACI)
Surface treatments and applied corrosion inhibitors, including amino alcohol-based (AMA) inhibitors, only make the surface of the concrete structure waterproof – and in some cases, merely water-resistant. Even then, effectiveness is completely reliant on the application process – uneven coatings or improperly applied treatments can completely ruin any waterproofing reliability. These treatments also wear off or become porous over time, requiring costly maintenance or complete reapplication.
Hydrophobic Admixtures
Recent ASTM Testing Results:
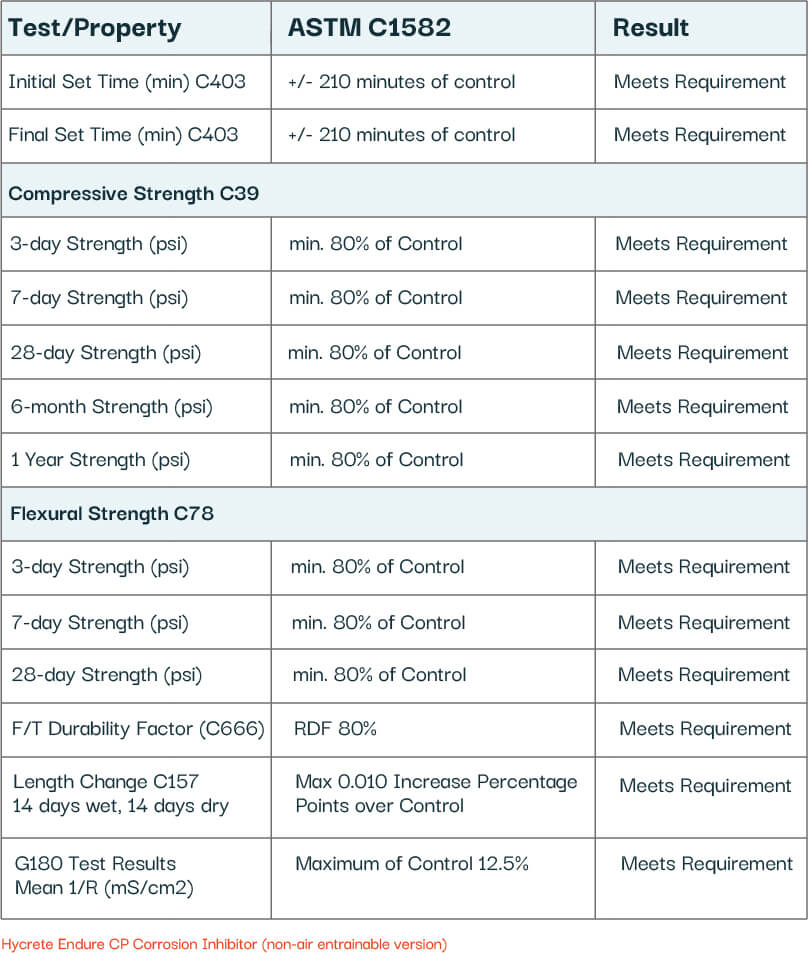
See more about Hycrete’s recent testing results.
In contrast to the above methods, Hycrete’s hydrophobic admixtures make the concrete material itself waterproof. There are no treatments to wear off, no membranes that can leak, just surface-to-rebar protection against water and corrosion. While competing crystal growth products claim to prevent corrosion, they do not meet ASTM C1582 standards like Hycrete.
Hycrete is a dual-action hydrophobic engineered to keep water out of concrete while preventing corrosion – from the surface of the structure down to the rebar. The chemically advanced admixture forms a co-polymer throughout the concrete, filling virtually all pores and capillaries for a truly watertight solution. Simultaneously, Hycrete reacts with the metallic ions in concrete and rebar to form an internal corrosion-inhibiting surface coating around steel reinforcement.
Engineered to extend the lifetime of the structure, no re-application is required. Hycrete gives builders permanent protection for lifetime reliability and a better ROI.
Engineering the Most Effective Concrete Corrosion Inhibitor and Waterproofing Solution
Hycrete has become the first name in chemically-advanced hydrophobic concrete protection. Our admixtures are rigorously tested and scientifically proven to achieve better longevity, better sustainability, and a better ROI in new construction.